Cake Storage Hopper for Filter Press
- Core parameters
- Mud Storage: 3.5-12 m³
- Total Weight: 1015-3500 Kg
Product Introduction
Cake storage hopper for filter press is used to collect the unloaded filter cake, which can provide convenience for centralized transportation. The size of the cake storage hopper can be customized according to model of filer press and customers' requirements. Its opening modes are electric and pneumatic.
Product Features
It is unique in structural design, material selection, manufacturing process and anti-corrosion treatment. And it has the advantages of firmness,durability and strong practicality. It can collect filter cakes effectively, so as to provide convenience for filter cake treatment and decrease labors working strength.
Structure Diagram
Application
It is widely used in petroleum, chemical industry, dyestuff, metallurgy, papermaking, coal washing, sewage treatment and other fields requiring solid-liquid separation.
Parameters
Model |
Reserve Volume |
Total Weight |
Electric Putter Motor Power |
Number of Storage Hopper |
Boundary Dimension (mm) |
||
L |
B |
H |
|||||
CND03.00 |
3.5 |
1015 |
1.1 |
1 |
3000 |
1200 |
1800 |
CND04.00 |
4.5 |
1307 |
1.1 |
2 |
4300 |
1350 |
1845 |
CND06.00 |
6.0 |
1682 |
1.1 |
2 |
4500 |
1400 |
2400 |
CND08.00 |
8.0 |
2680 |
1.1 |
2 |
6450 |
1400 |
2750 |
CND12.00 |
12.0 |
3500 |
1.1 |
3 |
9600 |
1700 |
3200 |
OPTIONALS OF THE CUSTOMER'S CHOICE
Cake Dryer
The Cake Dryer is a 100% automatic system for the drying of the cakes of mud through the use of compressed air. The system is similar to the Core Blow; the jet of compressed air is blown into the central hole of supply of the plates, thus allowing a drying of block 20 plates, to have a final cake completely dry.
Watch the videoCake Washing
Cake Washing is a closed-loop system for special slurries containing chemicals. It is usually used in conjunction with membrane plates, allowing clean water to flow into the plate chambers before the bricks are discharged. This process rinses the bricks, lowering the level of chemicals below the threshold that would make them ‘special sludge’ with the associated disposal costs.
Watch the videoCore Blow
Cake Washing is a closed-loop system for special slurries containing chemicals. It is usually used in conjunction with membrane plates, allowing clean water to flow into the plate chambers before the bricks are discharged. This process rinses the bricks, lowering the level of chemicals below the threshold that would make them ‘special sludge’ with the associated disposal costs.
Watch the videoDrip Tray
The Drip Tray system consists of one or two staggered trays that occupy the part underneath the filter press during the filtration phase and collect the water droplets that escape. Once the filtration phase is over, the trays are then moved by a motor to allow the removal of the cake. This system is designed to prevent some of the water droplets escaping from the cloths from falling on the already discharged mud bricks.
Watch the videoReal Washing
The filter press can be equipped with an automatic plate and cloth washing system. The Real Washing system consists of a valve and piping system on the feed side of the filter press and vent valves on each plate. The feed pump sends clean water to wash out the residual sludge. The system washes the plates 20 at a time. The frequency of the washing cycle is set on the control panel.
Watch the videoRobo Wash
The Robo Wash is a fully automated canvas washing system that can be put into operation at the push of a button. The high-pressure sprayer, located at the end of a sliding curtain, runs between each plate and dispenses high-pressure washing water over the entire surface of the canvas, dislodging and removing any build-up of dirt on the canvas.
Watch the videoSqueezing Membrane
The Squeezing Membrane system allows better mechanical pressing of the sludge cake. Basically, the membrane is inflated with water and grows in volume by squeezing the sludge that is pumped into the chamber. A variable volume is the main difference to standard plates. The special plate, together with the drainage system, guarantees a drier end product and a more efficient filtration cycle. The draining of the cake also benefits. The material of the membrane can be varied by using different technopolymers depending on the customer’s needs and the material to be processed; they are usually made of polypropylene.
Watch the videoTilt Sensor
The Tilt Sensor system consists of upper and lower proximity sensors that control the tilt of the last closing plate. In the software that manages the filter press, the delay time between the two sensors can be set. If the second sensor is activated within the set time after the first, the machine can continue its cycle normally. If not, an alarm will be triggered.
Watch the videoTorbidity Sensor
The Torbidity Sensor is placed in the clear water storage tank and consists of a candle gauge (sensor) immersed in water with dissolved particles. Based on the feedback from the sensor, it is possible to determine where to direct the water flow. Using predefined values, if an excessively high turbidity level is detected, the system activates the valves and diverts the water flow from the fresh water tank to the wastewater collection tank, in order to put the water through the clarification phase again.
Watch the video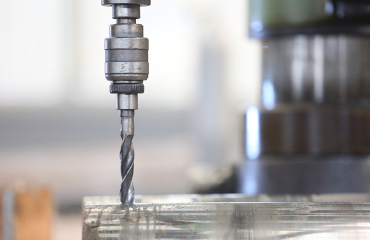
BBNEP Raw Material Analysis Laboratory
Technique leads advance and innovation drives development
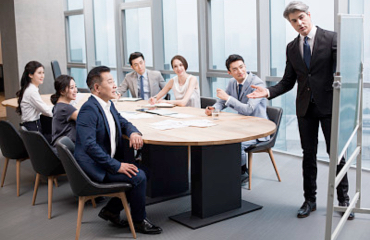
Targeted research on 12 industries
Achieving sewage discharge standard and realizing recycling